MEDATech Borterra’s RodBot™ is a robotic drill-rod handler that boosts workplace safety. Designed specifically for loading and unloading drill rods and casing, RodBot cuts manual rod handling by 95% and reduces the number of people needed on a drill rig, in most cases, to a single operator.
Created by MEDATech’s Borterra drilling division, the hydraulic, robotic pipe handler is suitable for mining, construction and the oil & gas industry, as it can be adapted to work on virtually any piece of drilling equipment. Mounted to a drill rig, pipe truck or on a skid, controlling RodBot is about as challenging as your average video game. Its computer-assisted controls come with embedded collision-avoidance capabilities, increasing safety.
With RodBot, pipe and casing is picked up or put into the cradle with a precisely-controlled grapple, or magnets. Once the operator has manually steered the pipe or casing to or from the mast, they can essentially hit ‘repeat’ and RodBot adds or removes rod or casing as needed.
RodBot is industry-leading in that it’s 100% hydraulic-robotic. The technology is similar to what automotive manufacturers have been employing on lines for over two decades, but in a remote setting. Since Borterra’s software is what does the heavy lifting, RodBots can be built to spec for any size of pipe.
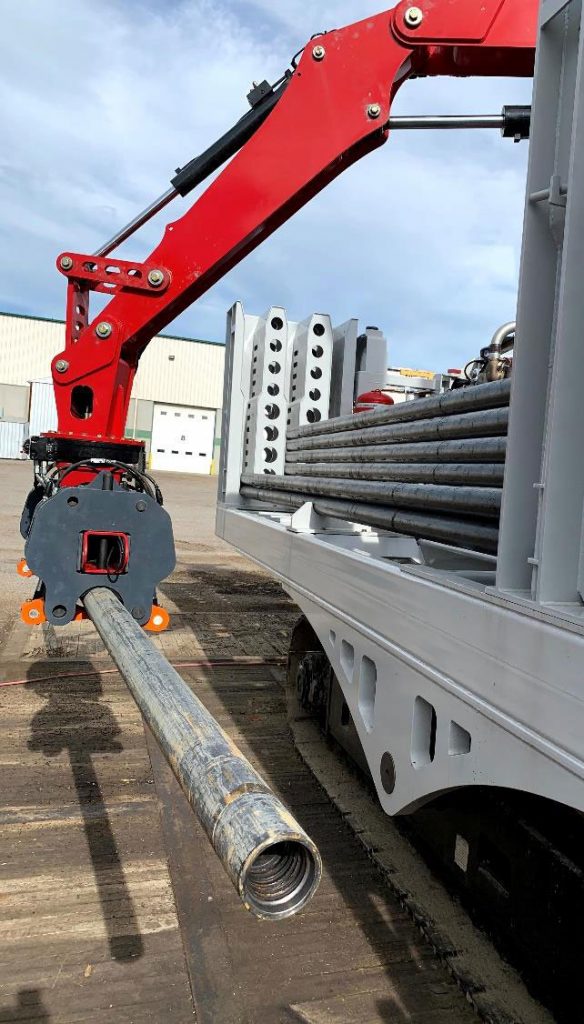
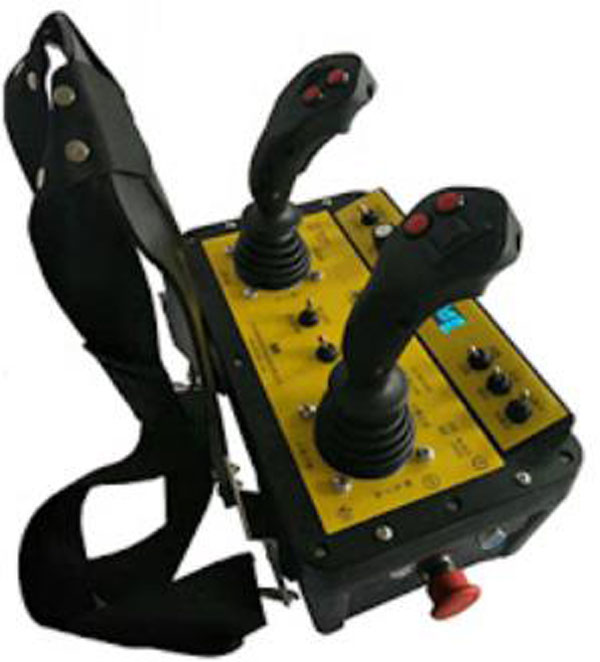
RodBot has three control modes: from Full Manual, where the operator controls movement every step of the way, to Autonomous Control with Collision Avoidance.
- Full Manual Control The operator has manual control of each moving element of the arm
- Tip Control. Computer assistance allows the operator to control the arm moving the drill pipe in a linear motion. Single-axis input on the joystick translates to the pipe, moving in a straight line either vertically or horizontally out from the arm base.
- Autonomous Control (User-Defined Path). The RodBot moves along a path determined by the operator and/or automatically adapted to the current mast position. The operator has hands-on control and can start/stop at any time if safety is ever in question.
Collision avoidance
RodBot has what robotics engineers call “go” and “no-go” areas: zones within the arm’s reach in which it’s safe to operate and zones where it’s not. That includes defining zones where there is equipment in the way and must be avoided. With RodBot, an operator can program a starting point, an ending point, and the robot will calculate the most efficient path, including navigating around any defined obstacles, using collision-avoidance software built into the robotic operating software.
As a separate unit, RodBot can mount to an existing drill rig or be set beside the drill on a skid. The operator can define and modify no-go zones for both the path taken by the robotic arm and exclusionary zones for the drill setup at each new location.
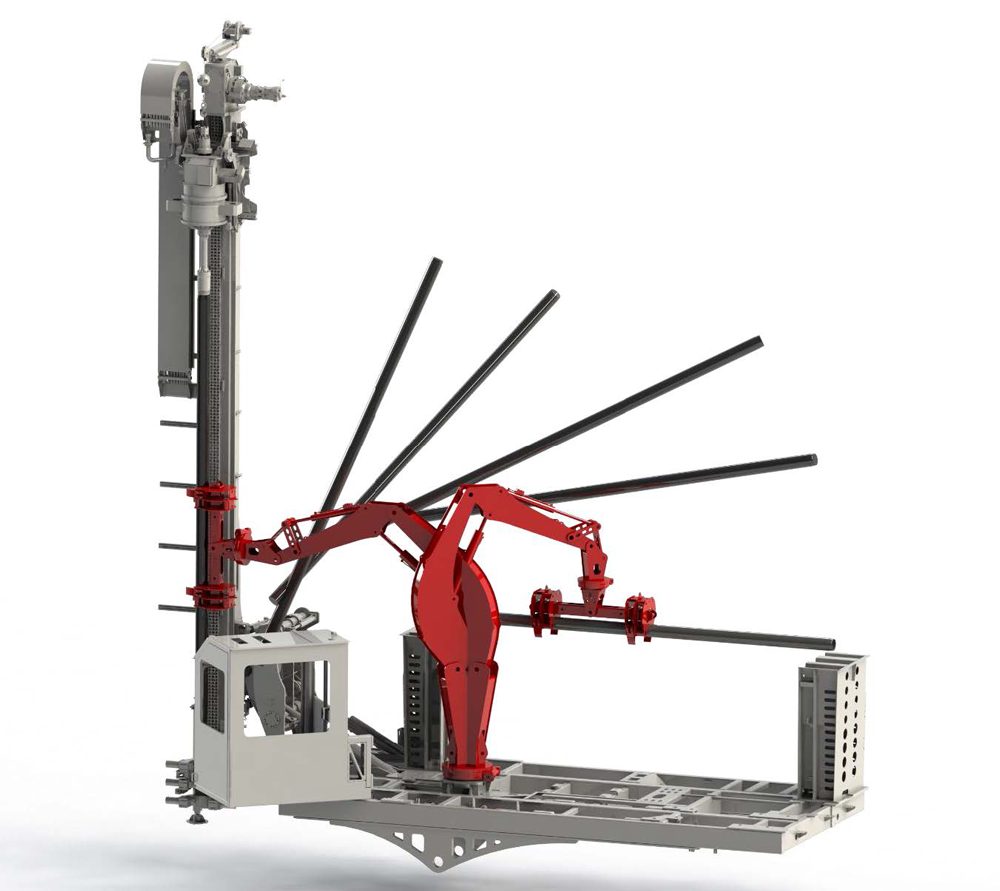
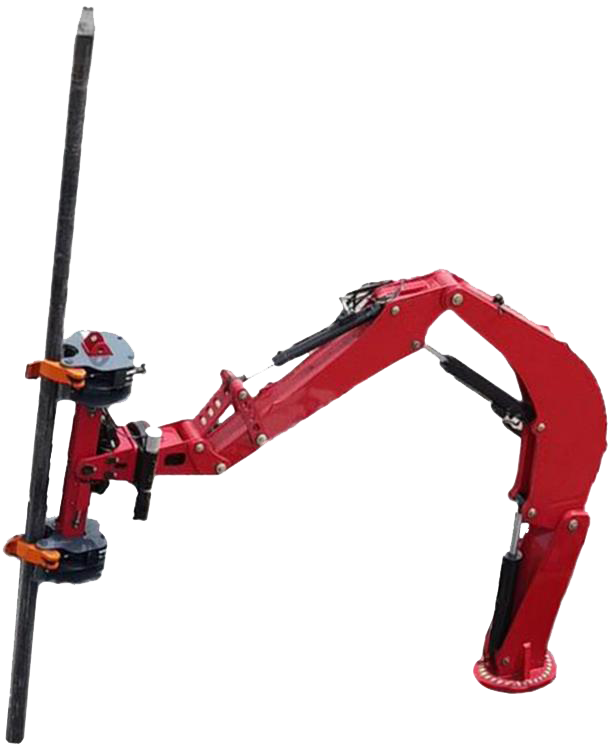
RodBot retrofits
There’s no need to wait for drill rig replacement to start using RodBot, as it can be retrofitted onto most rig configurations. Borterra can also supply a dedicated hydraulic powerpack (diesel, gas, or electric), help integrate your existing hydraulic system, or supply you with the information you need to do it on your own.
If worker safety and production speed are important to your organization, view our live demonstration at medatech.ca/rodbot or contact us at (705)-443-8440 or [email protected].

If worker safety and production speed are important to your organization, view our live demonstration at www.medatech.ca/rodbot or contact us by using the form below. We will be in touch very shortly.