How to choose the best industrial lithium battery
I recently returned from a large equipment Expo. My goal there was to understand the state of the heavy equipment industry with respect to adapting EV (electric vehicle) technology. There were several machines on display billed as either “Hybrid” or “Electric” but what really caught my attention was that although the industry is beginning to adopt lithium batteries, OEM’s are not properly educating the consumers about the differences between lithium battery types.
At one demonstration, for example, a machine was pitched as using the “latest in lithium battery technology”. I asked what they were referring to as the “latest” in this technology? Were they using lithium-titanate or lithium nickel manganese cobalt? Or was it lithium iron phosphate?
The salesman, of course, had no idea. Like so many OEM’s, his company was relying on the fact that consumers aren’t even aware that there is a difference between lithium batteries.
Worse still, most OEM’s aren’t actually using the latest in lithium technology at all. Many of them are building their own batteries or relying on artisan-type battery producers that haven’t fully developed the technology they use. There is a significant safety concern with these batteries and, many battery systems today look like they were cobbled together with jumper cables sourced from the local hardware store. Far too many companies today are, literally, playing with fire!
As both an advocate and a user of the technology, I felt compelled to write a post to educate consumers about the differences between these batteries.
This article will also help you know what to look for in a battery to ensure you are getting a good product, and give you some guiding principles for dealing with manufacturers and suppliers. I’ve broken it into three parts:
- Battery Chemistry 101: A brief overview of battery cell chemistry, and the concepts you need to understand.
- Popular Battery Types: A look at three common industrial lithium battery types, and their pros and cons.
- Strategies for Choosing: Four ways to help you make better decision when looking at equipment and dealing with OEM’s.
I. Battery Chemistry 101
Lithium is only half the story. You need to understand the chemistry of the entire cell because a difference in chemistry results in a significant difference in performance, cost and life.
Four key concepts need to be understood in battery technology.
1 – Energy Density– For the same volume of battery how much energy can it store.
2 – Power Density– For the same volume of battery how much power (kilowatts) can it deliver.
3 – Cycle Life– Is the amount of times you expect to Discharge the battery before you see a decrease in its performance. Automotive 300 Cycles vs. Industrial 10,000 Cycles.
4 – C-Rate– Same as Power Density. Batteries are limited by their C-Rate, which governs how fast they can charge and discharge their power. The capacity of a battery is commonly rated at 1C, meaning that a fully charged battery rated at 1Ah should provide 1A for one hour. The same battery discharging at 0.5C should provide 500mA for two hours, and at 2C it delivers 2A for 30 minutes.
II. Popular Lithium Ion Battery Types
LiNiMnCoO2 (NMC)
Lithium Nickel Manganese Cobalt Oxide, or NMC, is the current champion for energy density, coming in with a range between 150-220Wh/kg. Thanks to recent advances in cathode design, the power density or “C-rate” of this chemistry can range from 1-5C.
The automotive industry is using a relatively cheap version of this chemistry, which allows for long distance travel but with a short cycle life (typically around 300 cycles). The same chemistry can be tweaked to favor power output and an increased cycle life of up to 10,000 cycles.
LiFePo4 (LFP)
Lithium Iron Phosphate, or LFP, is the cheapest of the current lithium battery chemistries used in industry. A good LFP has an energy density between 90-110Wh/Kg, which is about half of the NMC chemistry.
Strictly speaking these batteries are relatively safe and sometimes are used as a higher performing lead acid battery. A drawback of these batteries is they have a limited “C-rate” of around 1C, which means they take a long time to charge.
I have seen several variants of these batteries in use, but I have yet to see one perform adequately as a replacement for a diesel engine. It’s imperative to get an LFP with a good temperature management system (TMS).
Li4Ti5O12 or LTO
Lithium-titanate, or LTO, can be fast-charged and will deliver a high discharge current of 10C, or 10 times the rated capacity. The cycle count is said to be higher than that of an LFP Battery.
Lithium-titanate is safe, has excellent low-temperature discharge characteristics, and has a capacity of 80 percent at –30°C (–22°F). However, the battery is expensive, and at 65Wh/kg the specific energy is low.[2] I’m keeping my eye on this technology, but for now it doesn’t appear to be ideal for industrial applications.
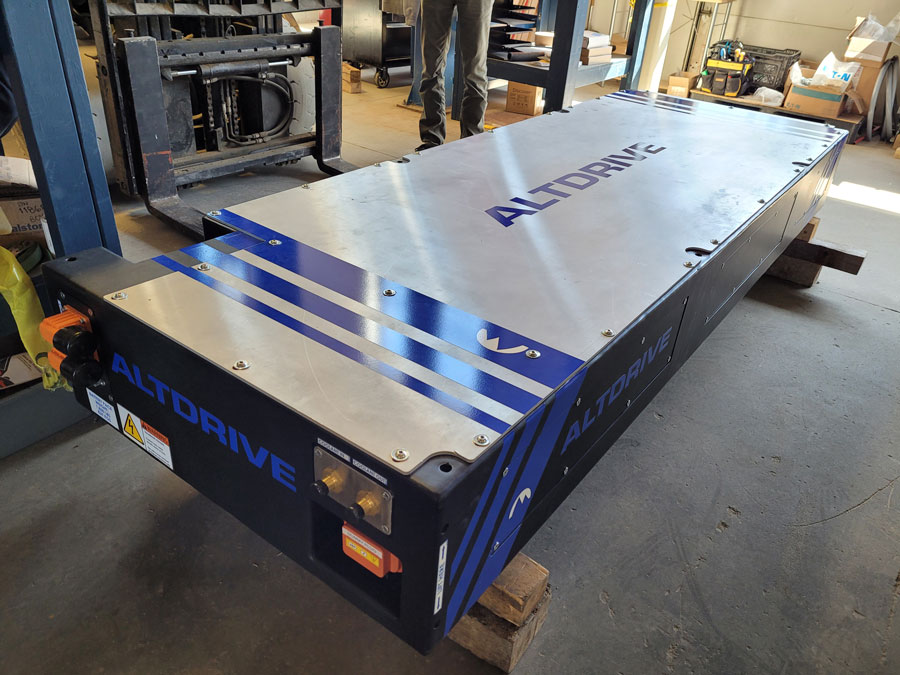
III. Strategies for Choosing the Best Industrial Lithium Battery
I use the following criteria when I rate a battery or source one for a customer. It is by no means comprehensive, but if a supplier can’t answer your questions in these areas, then they’re not worthy of your business.
Choose Safety over Price
- There’s a wide cost and safety spectrum in the battery technology to choose from. My advice is to pay the premium. Battery accidents are dangerous, and in my experience, more expensive in the long run than buying safe, quality batteries in the first place.
- Ask suppliers for stats on incidents, or ask to speak to other customers who have used the same battery for a long period of time.
Check Cooling and Temperature Management
- Lithium batteries are like humans; they like to work around 25°C. Temperature and battery management systems (TMS and BMS) are the most significant part of the batteries design. High and low temperatures lead to decreased performance and can mean permanent damage.
- Off-gassing is the last step before a fire, and results in permanent damage to the battery. If you’ve heard of a supplier’s battery off-gassing, this is a big red flag.
- Liquid cooled systems allow for conditioning, which means you can heat and cool the liquid going to the battery. That allows for optimal performance at any ambient temperature.
- Stay away from batteries with no active temperature management systems.
Look Closely at Physical Packaging
- Look for printed circuits, not loose wires. The more wires visible and present, the higher the likelihood of a failure.
- Ask about fire containment and fireproofing of the cells. The best companies have planned for a fire and have safety systems in place that ensure it’s contained.
- Look to companies that have made considerable efforts in cooling. This is probably the single biggest differentiator in battery management—I can’t stress this enough.
- It should be extremely hard to access the battery’s cell. These are high voltage and high amperage systems that should not be exposed to the elements. The more redundancy in the design of the packaging the better.
- Plastic or molded parts suggest high volume. Moreover, molded aluminum parts suggest a big investment from the manufacturer into the high-volume supply of their systems.
- Stay away from battery systems that are custom built for your application. Something modular that is used in multiple industries is your best bet.
- Efforts in insulation go a long way to managing the performance of the battery. Look for insulated containers and cellular packaging.
- Modularity in design means redundancy and safety.
Check Experience, Field Performance and Fine Print
- Many equipment manufacturers who make their own batteries have built at most dozens of batteries. The big players in battery tech, on the other hand, have thousands of reference customers and applications. Don’t be fooled into thinking that experience in the equipment’s application translates into knowledge of batteries. These are complex systems and are not easily perfected.
- Published cycle life is usually indicated as a percentage of DoD “Depth of Discharge”. The standard is to provide cycle life as a measure of 80% DoD. Anything less than 80% misrepresents the life of the battery.
- Ask the manufacturer if the cycle life is theoretical or measured. Is it measured in a lab or proven in the field? Only a select few companies have proven data from field applications since the technology has only been commercially available for a short period.