The first practical, important move towards emissions reduction is often moving to a hybrid diesel/battery-electric powertrain. Hybrid systems pair the energy density of diesel with the flexibility of electric power, extending range and reducing fuel consumption by 30% to 50% or more.
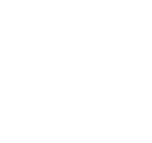
Improved fuel efficiency & lower emissions
Diesel extends vehicle operating range beyond battery-electric only operation
Hybrid vehicles consume 30% to 85% less diesel for the same workload
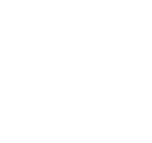
Reduced battery requirement
Less battery reduces weight and space requirements, as well as capital costs
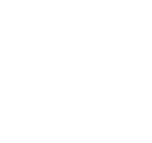
Extended range
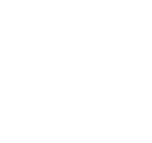
Reduced charging infrastructure
Little to no battery charging infrastructure (charger, power source) may be needed with hybrid drives
In 2023, worldwide battery cell manufacturing capacity was approximately 2.2 terawatt-hours. In ensuing years, that number will have risen about 33% per year. And that still isn’t likely to keep up with demand.
While consumer EV adoption around the world is brisk, industrial adoption is not. All-electric industrial vehicle fleets may be the future, but getting there isn’t simple. Batteries are expensive, heavy, and take up lots of space on machines. Pound for pound, batteries haven’t yet approached the energy density of diesel. When you add the huge electrical power needs of big industrial machines, power management and charging, the idea of an all-electric industrial fleet management can be daunting.


The first practical move towards CO₂ reduction
While big industry is experimenting with battery-electric, management teams have trouble seeing a clear path to both electrification and profit. But with increasing regulatory pressure and corporate mandates to reduce emissions, industrial businesses like mining, forestry and construction are turning to hybrid powertrain solutions to help meet sustainability goals without compromising performance. Batteries can play an important role in reducing the amount of diesel burned by heavy-duty mobile equipment when they form part of a hybrid powertrain.
The first practical, important move towards emissions reduction is often moving to a hybrid diesel/battery-electric powertrain. Hybrid systems pair the energy density of diesel with the flexibility of electric power, extending range and reducing fuel consumption by 30% to 50% or more. With that comes a corresponding reduction in emissions and operating costs. These and other benefits make hybrid technology the practical choice for heavy-duty vehicle fleets that are on the road to full-electric fleet conversion.

Current diesel engine: generator and range extender
In a hybrid diesel/electric powertrain, the diesel engine serves as a generator that charges batteries, while the electric motor or motors power the vehicle directly. This applies both to purpose-built hybrid powertrains and retrofit vehicle conversions that keep the original diesel engine.
Running at an optimized, steady RPM, the diesel engine maintains peak efficiency, delivering steady power to the battery bank that directly powers vehicle systems. As a result, less fuel is consumed over the course of a shift. And where a battery-only vehicle might need recharging several times per shift, the range of hybrid vehicles is normally only limited by the size of their fuel tanks.
Hybrid powertrain configuration
Hybrid diesel/electric powertrains can be configured to turn off the diesel engine and switch to 100% electric power when workload requirements are low. Hybrid powertrains can also be configured to draw power from both the generator and the batteries when workload is exceptionally high.
Vehicle powertrain hybridization regularly reduces fuel consumption by 30% or more. It can reach 85% in highly cyclical duty cycles, where high power demands are brief and battery-electric power can handle the majority of the workload.

Duty cycle: the key to hybrid efficiency
The main factor in hybrid system efficiency is the machine duty cycle. Heavy-duty vehicles can experience periods of high power demand followed by lower demand phases. Hybrid diesel/electric powertrains capitalize on these variations, either by keeping the diesel engine ticking along at an optimal RPM and fuel efficiency, or by using electric power only during low-demand cycles and calling on diesel power for more intensive work.
By strategically balancing power sources, hybrid systems maximize fuel efficiency without sacrificing performance. In the case of machines that use braking, such as haul trucks descending grades, regenerative braking can recharge batteries, reducing the need for diesel-powered charging and potentially less brake maintenance.

MEDATech’s 3 Divisions

From consulting to software development & engineer/design/build

Specialty Drilling Solutions

Battery-Electric Powertrains