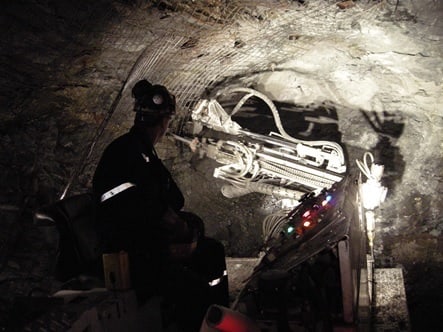
PROJECT
Camiro Micro Bolter
Customer: Vale Inco’s Coleman Mine
About The Project
The mining industry has an enviable record of overcoming engineering challenges, but one challenge that has baffled equipment designers and engineers until now is how to install a six- or eight-foot bolt in an eight-foot high drift using mechanized equipment. For an industry that relies on advanced technology for just about everything else, the use of hand-held jacklegs and stopers for the installation of ground support in narrow vein mines stands out as a throwback to an earlier era.
Now, this puzzle too has finally been solved following the successful trial of the so-called Camiro Micro Bolter at Vale Inco’s Coleman Mine in January. Designed and manufactured by Medatech Engineering Services of Collingwood, the Camiro Micro Bolter was championed by mining engineer Eric Hinton, a self-avowed advocate of mechanized equipment for micro mines. Hinton doesn’t buy into the mantra that bigger is always better, insisting “there are a lot of mines around the world that actually require much smaller equipment.
“We’ve backed miners away from the face by using larger equipment, but the larger equipment also requires larger openings and that meant that if the orebody narrowed significantly, you couldn’t really chase it anymore because there’d be too much waste.”
Moving material
Hinton, a former Inco employee currently employed by Golder Associates in Winnipeg, doesn’t blame the equipment manufacturers. It’s the mining companies themselves that have pushed for bigger machines. The priority, he said, has been moving more material. Appropriately sized loaders and production drills are available for narrow vein mining, but no one was pushing for a micro bolter, so Hinton called Medatech president Rob Rennie in late 2007 to take on the task. A mechanical engineer and former head of Maclean Engineering, a company widely known for larger format mechanized bolting equipment, Rennie at first turned down the invitation.
“In my previous career at Maclean Engineering, we built a micro bolter for Falconbridge, but they insisted on a certain speed on the ramp which demanded a lot of horsepower. The criterion to go that fast and have the thing mobile completely blew it out of the scope of what would fit in the working headings. As engineers, we made a few mistakes too, so when I was called and asked to do this, I said no, it can’t be done.”
Days later, he had a change of heart. Rennie was in the midst of doing some work for a diamond drill manufacturer and had designed some specialty components that struck him as being a possible solution for a micro bolter. He picked up the phone, called Hinton and agreed to put some ideas on paper. Hinton then called another old friend, Charlie Graham, managing director of Camiro, a Sudbury-based mining industry organization that manages applied, collaborative research. Graham persuaded Vale Inco, Xstrata, Barrick Gold, HudBay Minerals, Breakwater Resources and Teck Cominco to fund the project and the rest is history.
Health and safety
According to Rennie, the Camiro Micro Bolter isn’t about increasing productivity. “This machine is not as productive as two guys with jacklegs on a muckpile. It’s about safety, fatigue and giving the guys the right tool for the job.” Hinton couldn’t agree more, pointing out that jacklegs expose miners to falling ground and are linked to white hand syndrome, or Raynaud’s disease, which is caused by the constant vibration of the hand-held drills. “It’s a young man’s sport,” he said. “Once you get a little older, you find out how much it takes out of you. It’s very demanding.”
The Camiro Micro Bolter is an electric-hydraulic unit on crawlers. “It looks more like an in-the-hole crawler unit with a funny kind of folding table on the front and a boom that has quite a bit of dexterity to it,” said Rennie. “It’s not a mobile piece of equipment. It has to be put on a skid or towed from level to level, but it does move on its own when plugged into a 600-volt grid.”
The bolter has a comfortable chair, but is also equipped with wireless remote controls, allowing the operator to stand beside it. “It’s not hands-off by any means, said Rennie. “There is still some labour required to change the steel when you’re in a very low back, and you have to handle the screen and bolts. “In a nine-foot back, you can put in a six-foot rebar or bolt. In an eight-foot back, you have to drill a four-foot hole, and change to a six-foot steel to finish the job. I don’t know of any other machine that allows you to put in a six-foot bolt in that low a back.”
The design allows the operator to handle screen, bolts and steel under protected ground and provides easy access to the back to install screen hooks or resin cartridges without the aid of additional ladders.
Testing
The bolter was first tested at the NORCAT experimental mine in Sudbury, but only to fine-tune the unit mechanically. The true test occurred at Vale Inco’s Coleman Mine, where jackleg/stopper miner and jumbo driller Mike Morrison put it through its paces.
“He told us outright that he would treat the machine like he would treat any other machine. He had a very positive attitude and was absolutely phenomenal to work with,” said Rennie. “We’re not equipment operators. We’re engineers, and you can’t put an engineer who has never done that kind of work behind a piece of equipment like that.” A few design changes will be made as a result of the trial, but according to Rennie, the bolter performed the job as expected and qualifies as a technical success. The next step is to find someone to manufacture it and take it to market. “Achieving a technical success is fine. It’s thumbs up for me, but it would still be better if it were also a commercial success,” he said. “I’ll work with someone to make it happen and we might even make the first few units, but we’re not in the manufacturing business. Our focus is design and prototyping.”
The market for the micro bolter is limited, but would be of interest to a handful of mines in Northern Ontario, Quebec and Manitoba, said Rennie. Coleman Mine would need several units and Barrick would have an application for it in Nevada. Potential also exists for sales in Mexico, Peru, Brazil and Africa, but “they’d have to get over the cost issue.”